Products Gallery
HY Laser provides a wide variety of lenses catered towards laser marking, welding, cutting, scribing, medical care, and cosmetology. In the following, we have categorised our products with regard to the fields of industry application.
Browse Products:
All products are available for OEM customising service
Industry Application of Laser Lenses
Laser lenses in 3D printing play a crucial role in focusing and directing laser beams during the additive manufacturing process, especially in laser-based 3D printing methods such as Stereolithography (SLA) and Selective Laser Sintering (SLS). These lenses ensure that the laser beam is accurately concentrated onto the material, either to cure liquid resin or sinter powder layers.
Here is a demonstration of our lenses being used in 3D printing:
Basic Principles of 3D Printing
The basic process of 3D printing can be divided into three steps: modeling, slicing, and printing. First, the user needs to create a 3D model using CAD software. The model is then converted into formats like STL or OBJ so the 3D printer can recognize it. Next, slicing software divides the 3D model into layers and generates the printing path. Finally, the 3D printer follows the path to stack material layer by layer, completing the object.
Types of 3D Printing
- Fused Deposition Modeling (FDM): Uses thermoplastic filament, which is melted by a heated nozzle and then extruded layer by layer. FDM printers are relatively affordable and suitable for home and school use.
- Stereolithography (SLA): Utilizes liquid photopolymer resin, which is cured layer by layer using ultraviolet light to form solid objects. SLA printers offer high precision and surface quality, ideal for creating fine models. Our company specializes in producing field lenses and beam expanders, which are widely used in this area.
- Selective Laser Sintering (SLS): Uses powdered materials (such as nylon or metal powder) that are sintered together with a laser to form solid objects. SLS printers can produce metal, ceramic, and other high-strength materials, offering broad application potential.
Applications of 3D Printing
- Manufacturing: Used for prototyping, part manufacturing, and mold making, helping reduce product development cycles and costs.
- Architecture: Helps in creating architectural models and building components, aiding architects and clients in better understanding design plans.
- Medical Field: Used for creating dental prosthetics, hearing aids, bone implants, and customized drug carriers.
- Education: Used for producing teaching models, creative design projects, and fostering students’ hands-on skills and innovative thinking.
Practical Tips for Improving 3D Printing Quality
- Optimize Model Design: When designing models, avoid overly complex structures and reduce the use of support structures to improve printing efficiency and success rate.
- Adjust Printing Parameters: Set appropriate temperature, speed, and layer height according to the material and printing method to achieve optimal results.
- Regular Printer Maintenance: Keep the printer clean and well-maintained by checking the nozzle, transmission parts, and other key components regularly, replacing them as needed.
- Use Support Structures Wisely: Proper use of support structures can prevent model deformation and collapse during printing, improving the success rate.
Conclusion
As a revolutionary manufacturing technology, 3D printing is transforming how we produce and live. By understanding its principles, classifications, application scenarios, and practical tips for improving print quality, we can better harness this technology, unlocking endless possibilities for innovation and creation.
In 3D printing, particularly in laser-based additive manufacturing processes like Selective Laser Sintering (SLS), Fused Deposition Modeling (FDM)、Stereolithography (SLA), theta lenses (or f-theta lenses)、beam expanders play a significant role. Here are some key applications of optical components above in 3D printing:
1. Precise Laser Focusing
- Accurate Layer-by-Layer Fabrication: In 3D printing, theta lenses ensure that the laser beam is focused precisely on the powder bed, maintaining a uniform focal point across the build platform. This helps in fusing or sintering each layer of powder with high accuracy, ensuring well-defined part geometry and consistent layer thickness.
2. Wide Area Laser Scanning
- Large-Scale 3D Printing: Theta lenses enable the laser to scan a wide area across the powder bed without moving the print head, increasing the build area without compromising focus or beam quality. This allows for the efficient printing of larger parts in a single process, which is particularly useful in industries like aerospace and automotive.
- High Speed: By allowing the laser beam to be directed across the entire print bed without needing physical movement, theta lenses improve the scanning speed, enhancing the throughput of the 3D printing process.
3. Complex Geometry Printing
- Handling Intricate Designs: Theta lenses facilitate precise laser movement and focusing, enabling the creation of complex, highly detailed parts with fine features. In industries like medical devices or aerospace, where intricate geometries and fine tolerances are crucial, theta lenses help ensure the accuracy and detail required in 3D-printed parts.
- Variable Focus in Z-Axis: For printing complex parts with varying heights or curves, theta lenses paired with galvo systems allow for the dynamic adjustment of the laser’s focal point, ensuring proper energy delivery across different layers and heights.
4. Uniform Heat Distribution
Consistent Fusion Across Layers: Theta lenses help distribute the laser energy uniformly across the build platform, ensuring consistent heating and melting of the powder material. This prevents uneven material fusion, warping, or other defects in the printed parts, particularly important in metal 3D printing.
5. Multi-Laser Systems
Enhancing Throughput in Industrial 3D Printing: In some advanced 3D printing systems, multiple lasers are
Laser marking is a technique used to create permanent marks, patterns, or inscriptions on the surface of materials using a concentrated laser beam. It is a non-contact process that can be applied to a variety of materials, such as metals, plastics, ceramics, glass, and even organic materials like wood. Laser marking is widely used across industries due to its precision, durability, and versatility.
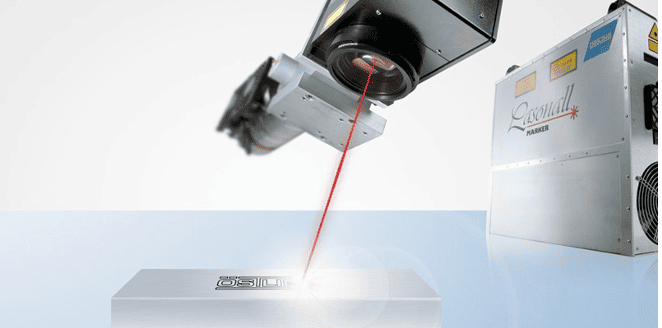
Key Types of Laser Marking
- Laser Engraving: The laser removes material from the surface to create deep, permanent marks or designs.
- Laser Etching: A variant of engraving where the surface is melted and expanded, producing shallow but durable marks.
- Laser Annealing: Often used on metals, this process heats the material to change its color, creating high-contrast marks without affecting surface smoothness.
- Laser Ablation: The laser removes thin layers of material, often used to remove coatings or top layers, revealing underlying material.
- Color Marking: This method involves adjusting the laser parameters to create color changes on materials like stainless steel or titanium without removing material.
Applications of Laser Marking
- Manufacturing and Product Identification: Marking serial numbers, barcodes, and QR codes on parts for traceability.
- Branding: Adding logos, labels, or product details to consumer goods.
- Medical Devices: Creating precise, corrosion-resistant marks on surgical instruments and implants.
- Aerospace and Automotive: Marking parts for identification, quality control, and regulatory compliance.
- Jewelry and Luxury Goods: Engraving intricate designs and personalization on metals and gemstones.
Advantages of Laser Marking
- High Precision: Allows for fine, detailed marks even on small surfaces.
- Permanent and Durable: Marks are resistant to wear, corrosion, and environmental factors.
- Non-Contact Process: The laser doesn’t physically touch the material, minimizing damage or distortion.
- Versatile Material Compatibility: Can be applied to metals, plastics, glass, wood, and more.
- Environmentally Friendly: No chemicals or inks are required, reducing waste and environmental impact.
F-theta lenses is our main product. We offer different types (different wavelength, focal length, entrance beam diameter , different material, also we can customize one according to customer requirements) of F-theta lenses.
An f-theta lens*(or fθ lens) is a specialized optical component commonly used in laser scanning systems, including laser marking applications. The primary function of an f-theta lens is to focus a laser beam onto a flat field in a manner that maintains a linear relationship between the scanning mirror’s angular displacement and the position of the focused spot on the marking surface. This ensures accurate, uniform marking across the entire field. Here are some key applications of f-theta lenses in laser marking:
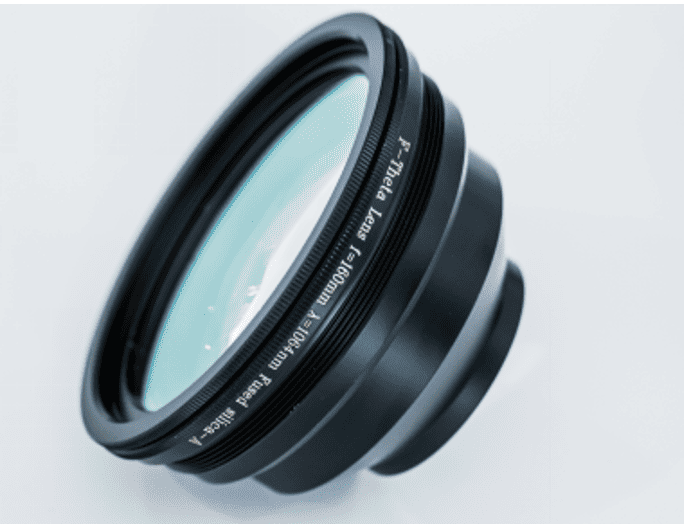
1. Flat-Field Scanning
One of the main applications of f-theta lenses in laser marking is to create a flat-field focus. As the laser beam moves across the marking area, an f-theta lens ensures that the focus remains sharp and consistent across the entire marking surface. This is critical in ensuring high precision and uniformity in laser marking for barcodes, text, serial numbers, and other designs.
2. High-Speed Laser Marking
F-theta lenses are used in high-speed laser marking systems due to their ability to focus the laser beam accurately and quickly over a wide field of view. The linear relationship between the scan angle and marking position allows for faster operation without the need for complex compensations, making them ideal for industries that require high-throughput production , such as electronics, automotive, and packaging.
3. Large-Area Marking
F-theta lenses are essential in systems that require marking over large areas without moving the workpiece. By focusing the laser across a broad flat field, these lenses enable marking machines to cover a large surface area efficiently. This is especially useful in batch processing or marking on large objects, such as metal sheets, plastics, or glass.
4. High Precision and Accuracy
In applications requiring high precision , such as microelectronics or fine engraving, f-theta lenses are crucial because they provide accurate spot positioning and minimize distortion. This accuracy ensures that detailed designs, logos, or small text are marked clearly and legibly.
5.Multiple Material Marking
F-theta lenses enable laser marking systems to work with a variety of materials, including metals, plastics, ceramics, and glass. By ensuring the laser’s focal point is consistent and well-defined, these lenses help in creating high-quality marks on materials that vary in hardness and reflectivity.
Laser welding and laser cutting are advanced manufacturing techniques that utilize focused laser beams to join or separate materials with high precision and efficiency. These processes are widely used across various industries due to their speed, accuracy, and ability to work with a wide range of materials.
Laser Welding
Laser welding is a method of joining two or more materials (typically metals or thermoplastics) by applying a focused laser beam to the joint area. The intense energy of the laser melts the materials at the surface, which then solidify to form a strong weld.
Key Features
- High Precision: The laser can be focused on small, intricate areas, enabling precise welds with minimal heat-affected zones.
- Deep Penetration: Laser welding can achieve deep, narrow welds, making it suitable for thick materials.
- Speed: The process is fast, allowing for high-throughput production, especially in automated systems.
- Low Distortion: Minimal heat input means less distortion in the material, important for applications requiring tight tolerances.
Applications
Automotive Industry: Welding car bodies, batteries, and other components with high-speed automation.
Aerospace: Creating lightweight, high-strength welds in aircraft parts.
Medical Devices: Joining delicate, corrosion-resistant materials for surgical instruments or implants.
Electronics: Welding miniature components like connectors and sensors.
Laser Cutting
Laser cutting involves using a high-powered laser beam to cut or slice through materials. The laser heats the material to its melting or vaporization point, and a gas (often oxygen or nitrogen) is used to blow away the molten material, creating a precise cut.
Key Features
High Accuracy: Laser cutting offers precise, clean cuts with fine tolerances, suitable for detailed designs and complex geometries.
Versatile Material Compatibility: It can cut metals, plastics, ceramics, wood, and even composites.
Minimal Material Waste: The non-contact process reduces material deformation and waste.
Efficiency: Laser cutting is faster and more efficient than traditional cutting methods, especially for intricate shapes or small parts.
Applications
- Metal Fabrication: Cutting sheets of steel, aluminum, or titanium for structural parts or industrial components.
- Electronics: Precision cutting of circuit boards and micro-components.
- Textiles and Plastics: Cutting patterns in fabrics or shaping plastic components in industries like fashion or packaging.
- Jewelry and Crafting: Intricate designs and personalization for small, delicate items.
We offer collimators, focusing lenses and protective windows for applications ranging from 3000W to 10,000W. It is suitable for various types of laser cutting heads and laser welding heads on the market. It is suitable for cutting all kinds of metal materials.
Those optical components play a critical role in laser cutting and welding by focusing laser beams accurately over a large field. Here are some key applications in these areas:
1. Precision Focusing and Beam Scanning
- Uniform Cutting/Welding: The theta lens is designed to maintain a consistent focal plane across the entire working area, ensuring that the laser beam remains focused regardless of its position. This is crucial in achieving uniform cutting or welding quality across large surfaces.
- Minimizing Focal Point Distortion: Theta lenses correct for distortions that can arise when scanning the laser beam across different angles, helping to maintain high accuracy and precision in both cutting and welding tasks.
2. High-Speed Laser Scanning
- Efficient Material Processing: In laser cutting and welding systems, f-theta lenses allow for faster scanning of the laser beam over the material. This increases the overall speed of operations, making it ideal for industries that need to cut or weld large quantities of material quickly, such as in automotive or aerospace manufacturing.
- Multi-Spot Welding: In welding applications, theta lenses are used in high-speed scanning systems to focus multiple laser spots across different areas, enabling simultaneous or rapid sequential welding of components.
3. Micromachining and Small-Scale Applications
Fine Detail Cutting: In micromachining or precision metal cutting, theta lenses allow for extremely fine, intricate cuts due to their ability to focus the laser beam into a very small, precise spot over a wide area.
Localized Heat Application: In welding, the theta lens ensures that the heat from the laser is applied only to specific areas, minimizing thermal distortion and ensuring high-quality welds in sensitive, high-precision industries like electronics or medical device manufacturing.
4. 3D Cutting/Welding with Galvo Systems
Complex Shapes and Depth Variations : Theta lenses are often paired with galvanometer (galvo) scanning systems, enabling precise control over laser movement in 3D cutting and welding tasks. This allows for the processing of materials with complex geometries or varying thicknesses, such as automotive parts or medical implants.
5. Large Field Laser Cutting/Welding
Broad-Area Processing: Theta lenses can be used in systems designed for processing large sheets of material without moving the laser source. The lens ensures that the beam remains focused across the entire surface, facilitating large-scale production such as in metal fabrication, where large metal sheets need to be cut or welded accurately.
Vision optics refers to the branch of optics dedicated to understanding and improving human vision, as well as designing optical systems that enhance or correct visual perception. This field combines principles of physics, biology, and engineering to study how light interacts with the eye and how optical devices can assist or correct vision-related issues. Vision optics encompasses everything from the fundamental study of how the eye processes light to the development of corrective lenses and advanced optical instruments.
Key Components of Vision Optics:
1. Human Eye and Visual Perception:
- Cornea and Lens: The eye’s cornea and lens act like an optical system, refracting light and focusing it onto the retina, where images are processed and sent to the brain.
- Refraction and Accommodation: Vision optics studies how the eye adjusts (accommodates) to focus on objects at varying distances and how refraction (bending of light) helps focus images.
2. Corrective Optics:
- Eyeglasses and Contact Lenses: These are designed to correct refractive errors such as myopia (nearsightedness), hyperopia (farsightedness), astigmatism, and presbyopia by altering the way light enters the eye.
- Intraocular Lenses (IOLs): Used in cataract surgery, these artificial lenses replace the eye’s natural lens, restoring clear vision.
3. Low Vision Aids:
- Magnifiers and Telescopic Lenses: Designed to help individuals with significant vision impairment by enlarging images or objects, allowing for better visual perception of details.
4. Advanced Optical Instruments:
Microscopes and Telescopes: These are used to magnify objects or capture distant objects, enhancing visual acuity beyond the natural limits of the human eye.
Ophthalmic Instruments: Devices like ophthalmoscopes, retinoscopes, and autorefractors are used to diagnose and assess eye health and vision quality.
5. Surgical Optics:
Laser Eye Surgery (LASIK): Corrects vision by reshaping the cornea using a laser, improving how light is focused onto the retina.
Optical Coherence Tomography (OCT): An imaging technique used to capture detailed images of the retina and other eye structures for diagnosing conditions like glaucoma or macular degeneration.
6. Optical Coatings and Filters:
Anti-Reflective (AR) Coatings: Applied to lenses to reduce glare and reflections, improving visual clarity.
Blue Light Blocking Lenses: Protect eyes from high-energy blue light emitted by digital screens, reducing eye strain and potential damage.
Our lenses in vision optics are widely used in the field of optical imaging, including industrial inspection, machine vision inspection, microscopy by focusing, bending, or spreading beams of light in a controlled manner. And we provide various types of telecentric theta lenses and we can design the overall optical path system in the operating microscope and provide customers with a complete set of lenses and solutions.
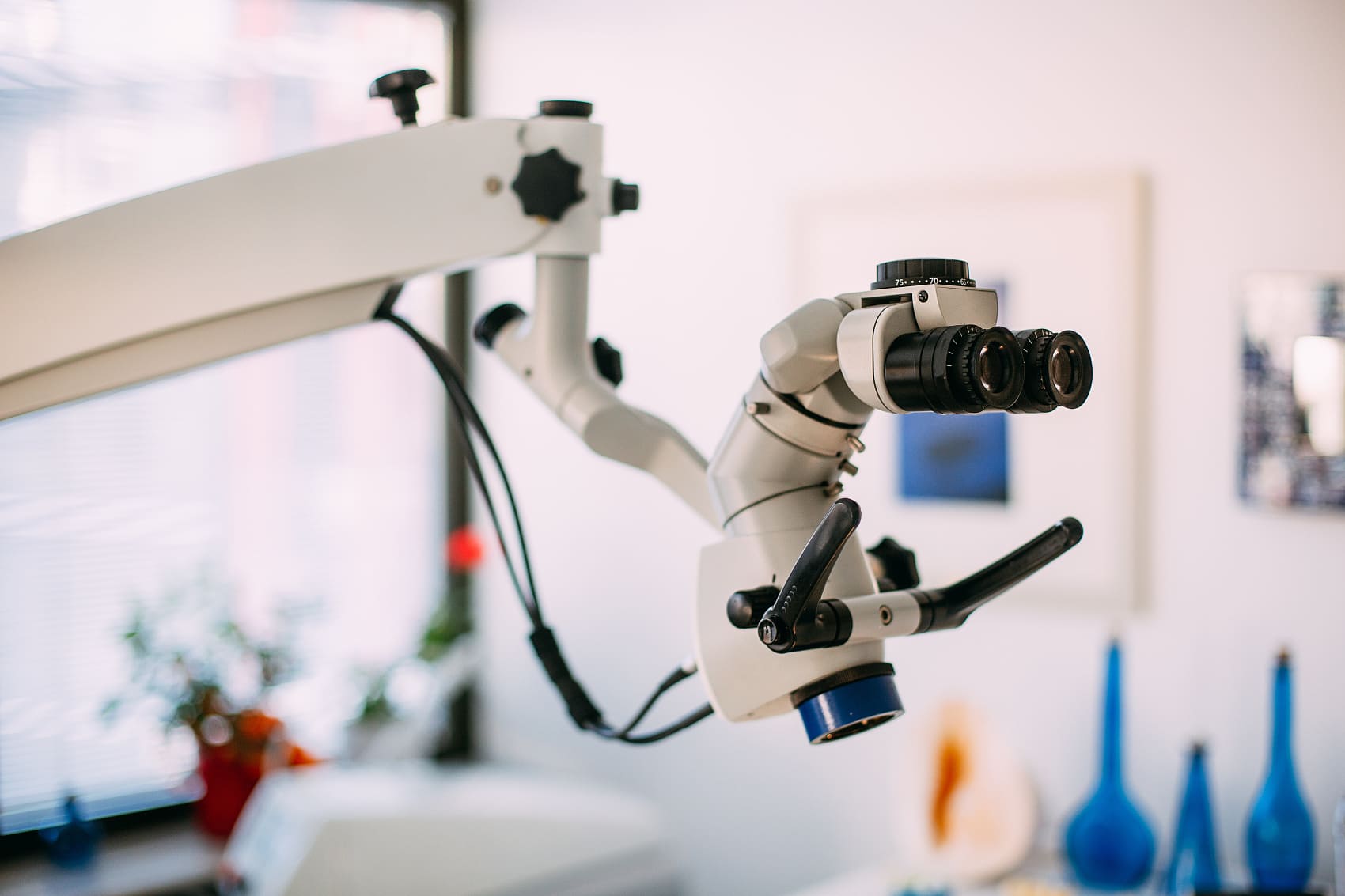
Microscopy
Microscopes use compound lenses (objective and eyepiece lenses) with high magnification power to resolve tiny details in specimens. These lenses are designed to minimize optical aberrations and provide high resolution and contrast, often using achromatic or apochromatic lens designs.
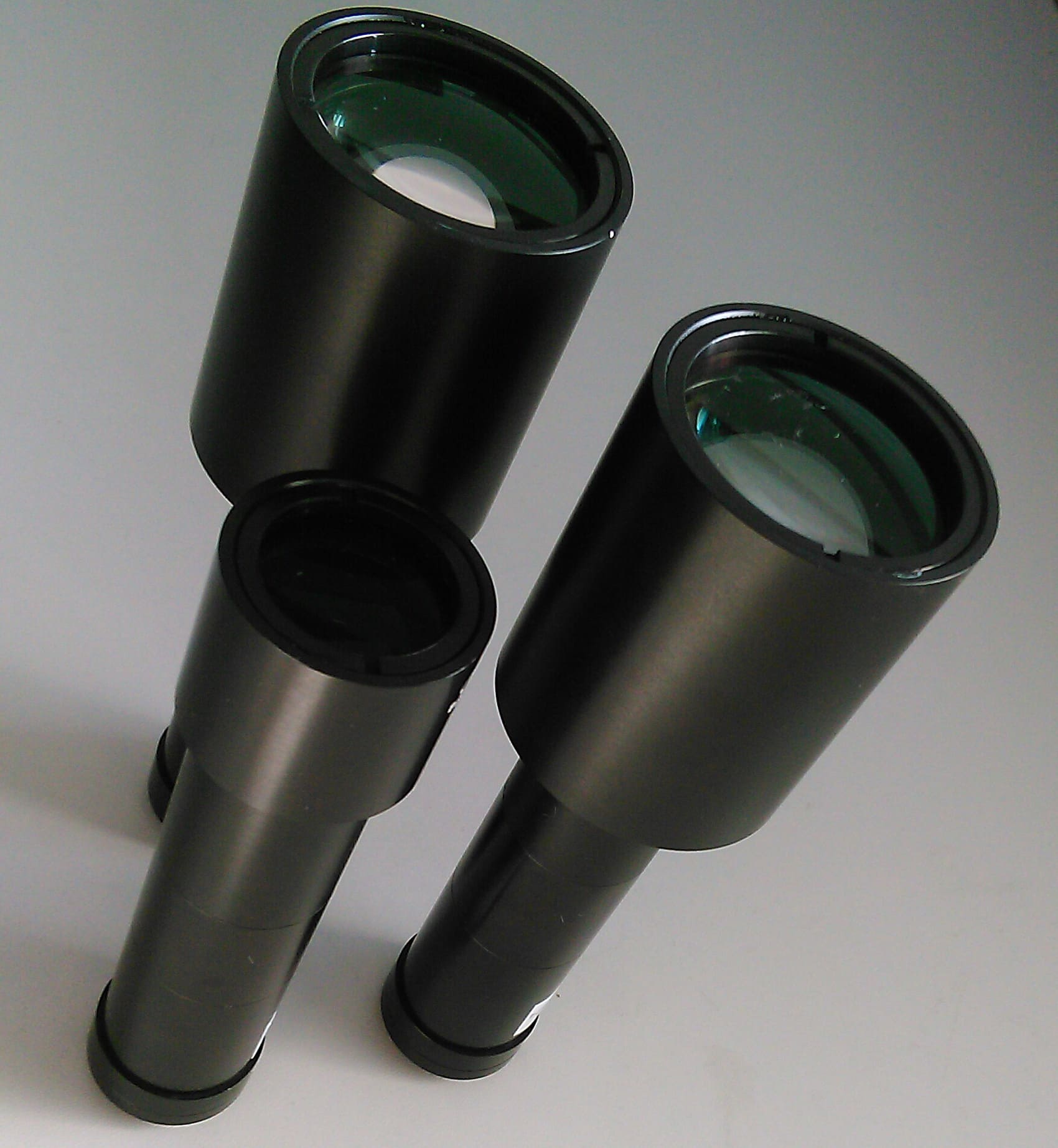
Vision Inspection
Telecentric theta lenses are specialized optical components used in inspection systems to achieve high-precision measurements and imaging. These lenses combine the benefits of both telecentric lenses (which maintain a constant magnification across different object distances) and theta lenses (which maintain a uniform focal plane over a large field of view). Their unique properties make them ideal for a variety of industrial inspection and quality control tasks. They are crucial in various industrial inspection applications where precision, accuracy, and distortion-free imaging are essential. Their ability to provide consistent magnification and clear, high-resolution images over a wide field of view makes them ideal for dimensional measurement, surface inspection, and automated quality control in industries like semiconductors, electronics, automotive, and medical device manufacturing.